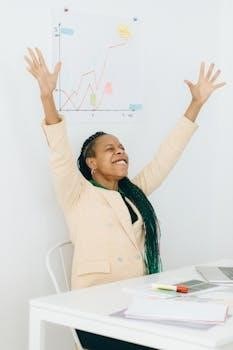
Welding Electrode Chart PDF⁚ A Comprehensive Guide
A welding electrode chart in PDF format serves as a handy reference tool․ It helps welders select the appropriate electrode․ The chart considers the base metal‚ welding position‚ and desired weld properties․ It provides amperage ranges and material compatibility information‚ all in one convenient document․
Welding electrode charts are indispensable resources for welders of all skill levels․ These charts provide a structured overview of various welding electrodes․ They assist in selecting the right electrode for a specific welding application․ The primary function of these charts is to match the electrode type with the base metal being welded․ This ensures optimal weld quality‚ strength‚ and durability․
Electrode charts typically include information on electrode classifications‚ such as E6010‚ E7018‚ and E316․ They also detail the recommended amperage ranges for different electrode diameters․ Furthermore‚ these charts may offer guidance on preheating and post-heating requirements․ These factors are crucial for achieving sound welds‚ especially with certain materials․
These charts are invaluable for both seasoned professionals and those new to welding․ They offer a quick reference for determining the appropriate electrode․ This reduces the risk of using an incompatible electrode that could lead to weld defects or failures․ Accessing these charts‚ often in PDF format‚ ensures easy portability and accessibility․ This makes them a vital tool in any welding environment․
Understanding Electrode Classifications
Decoding electrode classifications is crucial for selecting the correct welding rod․ Classifications‚ like E7018‚ provide vital information about the electrode’s properties․ The “E” signifies an electrode intended for arc welding․ The first two digits‚ in this case “70‚” indicate the tensile strength in thousands of pounds per square inch (PSI); This means the weld metal has a tensile strength of 70‚000 PSI․
The third digit reveals the welding position for which the electrode is suitable․ “1” denotes that the electrode can be used in all positions (flat‚ horizontal‚ vertical‚ and overhead)․ “2” indicates it’s suitable for flat and horizontal positions only․ The last digit specifies the type of coating and the welding current required․ For example‚ “8” indicates a low-hydrogen coating and the use of either AC or DC current․
Understanding these designations enables welders to choose the correct electrode․ This choice will ensure the weld meets the required strength‚ position‚ and application specifications․ Consulting a welding electrode chart PDF is essential for accurate interpretation․ This will ultimately lead to successful and reliable welding outcomes in various projects․
Mild Steel Electrode Types and Their Applications
Mild steel electrodes are widely used due to their versatility and cost-effectiveness in various welding applications․ The E6010 electrode is known for its deep penetration and is often used for welding dirty or rusty steel․ Its strong arc force makes it suitable for root pass welds․ E6011 is similar to E6010 but can be used with AC power sources‚ offering more flexibility․
E6013 is a general-purpose electrode that provides smooth arc characteristics․ It is ideal for thin sheet metal and applications where appearance is important․ E7014 offers high deposition rates‚ making it suitable for filling larger gaps․ E7018 is a low-hydrogen electrode‚ providing high-quality welds with excellent mechanical properties․ It is often used for welding thicker sections and high-strength steels․
Selecting the appropriate mild steel electrode depends on the specific application requirements․ Factors such as material thickness‚ welding position‚ and desired weld properties must be considered․ Consulting a welding electrode chart PDF ensures the correct electrode is chosen․ This will optimize weld quality and structural integrity across diverse projects․
E6010 and E6011 Electrodes⁚ Penetration and Usage
E6010 and E6011 electrodes are renowned for their deep penetration capabilities‚ making them ideal for specific welding applications․ E6010 electrodes are designed for use with DC (Direct Current) power sources‚ offering a forceful arc that penetrates through rust‚ scale‚ and other surface contaminants․ This makes them particularly suitable for field welding and pipeline construction where surface preparation may be limited․ They produce a dig-type arc that creates a deep‚ narrow weld profile‚ ensuring strong root pass welds․
E6011 electrodes‚ on the other hand‚ can be used with both AC (Alternating Current) and DC power sources‚ providing greater versatility․ They also offer excellent penetration characteristics‚ similar to E6010‚ and are often preferred when AC power is the only option available․ E6011 electrodes are known for their ability to weld through dirt and mill scale‚ making them useful in maintenance and repair work․
Both E6010 and E6011 electrodes require skilled welders due to their fast-freezing slag․ Mastering the proper technique ensures high-quality welds with the desired penetration depth‚ crucial for structural integrity․ A welding electrode chart PDF can assist in selecting the correct amperage range for these electrodes based on their diameter․
E7018 Electrodes⁚ Strength and Characteristics
E7018 electrodes are low-hydrogen‚ iron powder electrodes widely recognized for their superior strength and ductility in weld deposits․ The “70” in the designation indicates a minimum tensile strength of 70‚000 PSI‚ making them suitable for high-stress applications․ E7018 electrodes produce welds with excellent impact resistance and crack resistance‚ crucial for structural steel welding and heavy fabrication․
The low-hydrogen characteristic minimizes the risk of hydrogen-induced cracking‚ a common concern in welding high-strength steels․ E7018 electrodes require proper storage to maintain their low-hydrogen properties; they should be kept in a heated rod oven to prevent moisture absorption․ When welding‚ a short arc length and proper technique are essential to achieve the desired weld quality․
E7018 electrodes can be used in all welding positions‚ offering versatility for various projects․ They produce a smooth‚ stable arc and a relatively quiet operation․ The slag is easy to remove‚ contributing to efficient welding․ Consulting a welding electrode chart PDF helps determine the appropriate amperage range for E7018 electrodes based on electrode diameter and welding position․ Correct selection ensures optimal weld performance․
Stainless Steel Electrode Types (E316-15‚ 16)
E316-15 and E316-16 are popular stainless steel electrode types commonly used for welding austenitic stainless steels‚ particularly those containing molybdenum․ The “316” designation indicates the electrode’s composition‚ featuring chromium‚ nickel‚ and molybdenum‚ providing enhanced corrosion resistance‚ especially against pitting and crevice corrosion in chloride environments․ These electrodes are frequently used in chemical processing‚ pharmaceutical‚ and food processing industries․
The “-15” and “-16” suffixes denote the electrode’s coating characteristics and welding properties․ E316-15 electrodes typically have a lime-based coating‚ offering excellent arc stability and weld puddle control‚ primarily used with DC+ (direct current electrode positive)․ E316-16 electrodes have a rutile-based coating‚ providing smoother arc starting and operating characteristics suitable for both AC and DC welding․
Both E316-15 and E316-16 electrodes are designed for all-position welding‚ enabling versatility in various applications․ When selecting between these electrodes‚ consider the welding machine capabilities (AC or DC) and the desired arc characteristics․ Reviewing a welding electrode chart PDF provides valuable information on recommended amperage ranges and welding techniques for optimal results when working with stainless steel․
Electrode Size and Amperage Chart
An electrode size and amperage chart is an indispensable tool for welders‚ providing a quick reference for selecting the correct amperage range for a specific electrode diameter․ This chart typically lists various electrode sizes‚ such as 3/32″‚ 1/8″‚ 5/32″‚ and 3/16″‚ along with the corresponding recommended amperage range for each size․ Using the proper amperage is crucial for achieving a stable arc‚ proper penetration‚ and desired weld bead appearance․
Too little amperage can result in poor penetration‚ a weak weld‚ and the electrode sticking to the base metal․ Conversely‚ too much amperage can cause excessive spatter‚ burn-through‚ and undercut․ The electrode size and amperage chart helps welders avoid these issues by providing a starting point for adjusting their welding machine settings․ These charts often include information for different electrode types‚ such as E6010‚ E7018‚ and stainless steel electrodes‚ as each type has unique amperage requirements․
When using an electrode size and amperage chart‚ it’s essential to consider the specific welding application and material thickness․ Thicker materials generally require higher amperage settings‚ while thinner materials require lower settings․ Fine-tuning the amperage within the recommended range based on visual inspection of the weld is always recommended to achieve optimal results․ A welding electrode chart PDF can offer a convenient and readily accessible reference for this critical information․
Matching Electrode to Base Metal
Selecting the correct electrode for the base metal is crucial for achieving a strong‚ durable‚ and corrosion-resistant weld․ The electrode’s composition should be compatible with the base metal to ensure proper fusion and prevent metallurgical issues․ Using an incompatible electrode can lead to cracking‚ porosity‚ and reduced weld strength․
For mild steel‚ electrodes like E6010‚ E6011‚ E7018‚ and E7024 are commonly used‚ each offering different characteristics in terms of penetration‚ deposition rate‚ and weld bead appearance․ When welding stainless steel‚ it’s essential to use stainless steel electrodes such as E308L-16 or E316L-16‚ which contain chromium and nickel to match the corrosion resistance of the base metal․ Welding dissimilar metals requires careful consideration and often involves using a specialized electrode designed for joining specific metal combinations․
Consulting a welding electrode chart PDF is highly recommended to determine the appropriate electrode for a given base metal․ These charts provide comprehensive information on electrode compatibility‚ including recommendations for various steel alloys‚ stainless steels‚ and other metals․ They often include guidelines on preheating and post-weld heat treatment requirements‚ ensuring optimal weld quality and performance․ By carefully matching the electrode to the base metal‚ welders can create sound and reliable welds that meet the demands of the application․
Considerations for Preheat and Postheat
Preheating and post-weld heat treatment (PWHT) are crucial considerations․ They significantly influence the mechanical properties and integrity of the weld․ Preheat involves heating the base metal before welding․ This reduces the temperature gradient between the weld zone and the surrounding material․ It minimizes the risk of cracking‚ especially in high-carbon or alloy steels․
The preheat temperature depends on the base metal’s composition‚ thickness‚ and welding process․ Welding electrode charts often provide preheat recommendations for specific materials․ PWHT‚ on the other hand‚ is applied after welding to relieve residual stresses․ It improves ductility and toughness․ This process involves heating the welded component to a specific temperature․ It is held for a certain duration‚ followed by controlled cooling․
Electrode selection can be influenced by preheat and PWHT requirements․ Some electrodes are designed to be used with specific heat treatment procedures․ Improper heat treatment can lead to weld failure or reduced performance․ Therefore‚ consulting welding electrode charts and adhering to recommended practices are essential; They ensure optimal weld quality and prevent potential issues related to thermal stress and material properties․ These charts guide the welder in selecting the correct electrode and heat treatment for the chosen materials․
Welding Positions and Electrode Selection
Welding position plays a vital role in electrode selection․ The most common positions are flat‚ horizontal‚ vertical‚ and overhead․ Each position presents unique challenges․ Gravity affects the molten metal differently in each․ Flat welding (1G) is the easiest‚ as the molten pool is less prone to sagging․ Horizontal welding (2G) requires more control to prevent the metal from running down․ Vertical welding (3G) can be either uphill or downhill‚ each with its own set of electrode preferences․ Overhead welding (4G) is the most difficult․ It demands precise control and a fast-freezing electrode to combat gravity․
Electrode selection charts often specify suitable electrodes for each position․ Electrodes like E7018 are versatile․ They can be used in all positions with proper technique․ Others‚ such as E6010 and E6011‚ are better suited for specific positions due to their deep penetration and fast-freezing characteristics․ For out-of-position welding‚ electrodes with a fast-freezing slag are preferred to support the molten metal․ Understanding the characteristics of different electrodes and their suitability for various welding positions is essential for achieving sound welds․
Charts provide valuable guidance in this regard‚ ensuring that the correct electrode is chosen for the job‚ maximizing weld quality and minimizing defects․
Out-of-Position Welding Techniques
Out-of-position welding presents unique challenges․ It requires specialized techniques to counteract gravity’s effects on the molten weld pool․ Vertical and overhead welding fall into this category․ These positions demand greater welder skill and the use of electrodes designed for out-of-position work․ A key technique is controlling the heat input․ Excessive heat can cause the molten metal to sag or drip․ This leads to poor weld quality․ Using a shorter arc length and smaller diameter electrodes helps maintain control․ This allows for better manipulation of the weld pool․ Proper joint preparation is also crucial․ Ensuring a tight fit-up minimizes the amount of molten metal needed․ This reduces the risk of sagging․
Electrode selection is paramount․ Fast-freezing electrodes‚ like E6010 and E6011‚ are commonly used for vertical-up welding․ They solidify quickly‚ supporting the molten pool against gravity․ E7018 electrodes can also be used out-of-position․ However‚ they require more skill due to their slower freezing rate․ The “whip and pause” technique is often employed․ This involves moving the electrode forward and then quickly back; This allows the metal to cool and solidify slightly before adding more․ Consistent travel speed and angle are also essential․ They ensure uniform bead size and penetration․
Practice and experience are key to mastering out-of-position welding․ It’s important to understand the behavior of the molten metal and adjust techniques accordingly․
Electrode Selection for Specific Materials (A335 P1‚ A516)
Selecting the correct electrode is crucial when welding specific materials․ This includes materials like A335 P1 (low alloy steel) and A516 (carbon steel)․ The American Society of Mechanical Engineers (ASME) provides guidelines․ These guidelines help determine appropriate filler metals based on the base material composition․ For A335 P1‚ often used in piping systems‚ low-hydrogen electrodes like E7018-A1 are frequently recommended․ The “A1” designation signifies the addition of chromium and molybdenum․ These additions enhance the weld’s high-temperature strength and creep resistance․ Matching the filler metal composition to the base metal properties is vital for ensuring weld integrity․
When welding A516‚ a common pressure vessel steel‚ electrodes like E7018 are suitable․ E7018 offers good strength and ductility․ It also provides excellent weld deposit soundness․ Preheating may be required for thicker sections of A516 to minimize the risk of hydrogen-induced cracking․ The specific preheat temperature depends on the steel’s thickness and carbon equivalent․ Consulting welding procedure specifications (WPS) is always recommended․ WPS documents provide detailed instructions on electrode selection‚ preheat‚ interpass temperature‚ and welding parameters․
Always refer to material specifications and qualified welding procedures․ This ensures the selected electrode meets the required mechanical properties and service conditions․
Accessing and Using Welding Electrode Charts in PDF Format
Welding electrode charts in PDF format are readily accessible online․ Many welding supply companies and educational institutions offer these charts for free download․ A simple internet search using terms like “welding electrode chart PDF” will yield numerous results․ Ensure the chart is from a reputable source to guarantee accuracy․ Once downloaded‚ the PDF can be viewed on computers‚ tablets‚ and smartphones․ This makes them easily accessible in the shop or field․
Using the chart effectively requires understanding its layout and information․ Typically‚ charts are organized by electrode classification (e․g․‚ E6010‚ E7018)․ They include details on recommended amperage ranges for different electrode diameters․ The charts also specify suitable base metals and welding positions․ Some charts may also provide information on preheating and post-weld heat treatment requirements․ When selecting an electrode‚ first identify the base metal being welded․ Then‚ consider the welding position (flat‚ horizontal‚ vertical‚ overhead)․ Finally‚ consult the chart to find the appropriate electrode type and recommended settings․
Always double-check the manufacturer’s recommendations for specific applications․ Welding electrode charts are valuable resources‚ but they should be used in conjunction with sound welding practices․